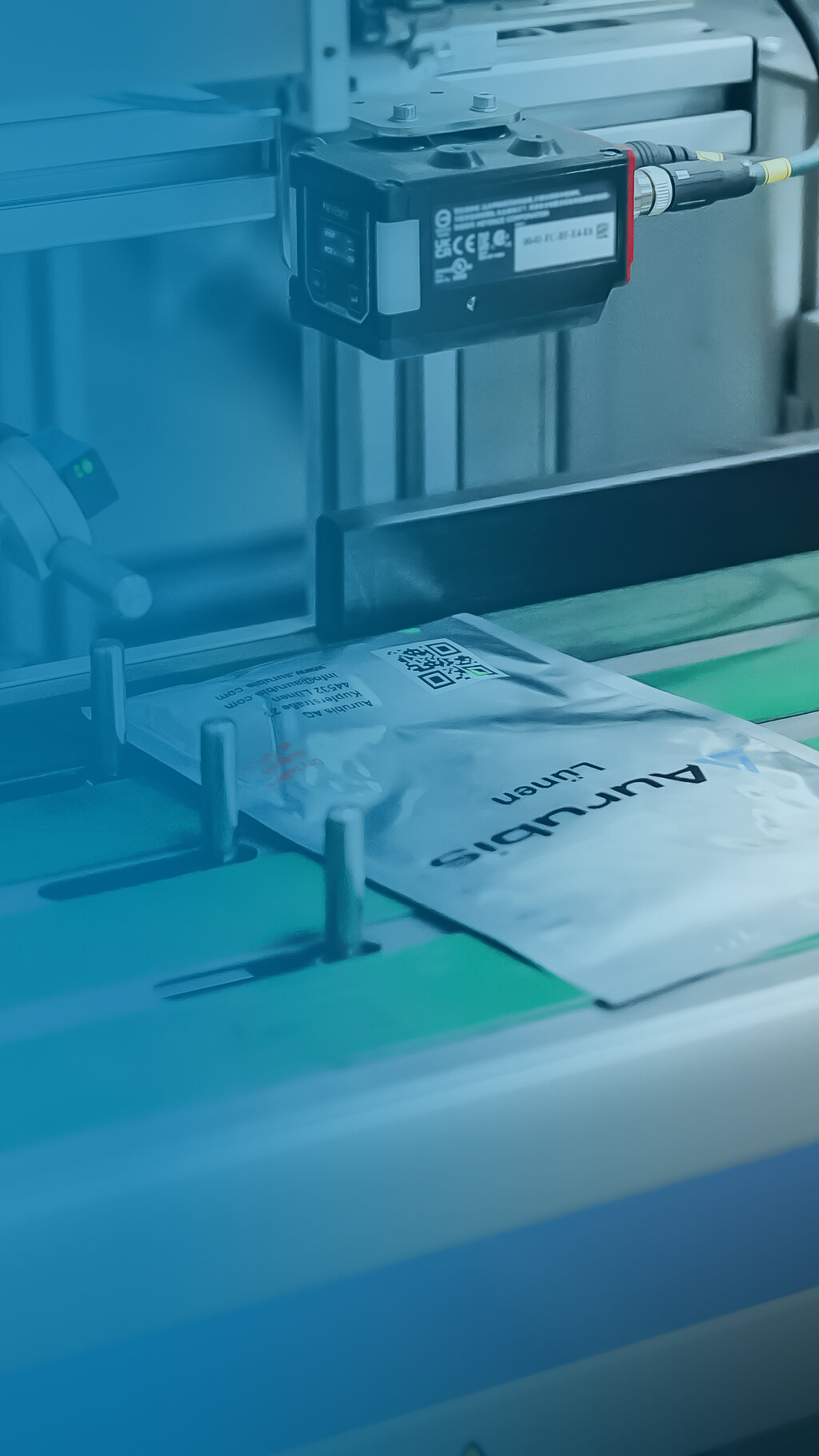
We drive
Innovation
Mit Pioniergeist und technologischer Exzellenz setzen wir neue Standards in der Metallindustrie. Wir schaffen effiziente, nachhaltige Lösungen für die Herausforderungen von morgen, indem wir die Automatisierung und Digitalisierung unserer Prozesse aktiv vorantreiben.
Automatische Probenaufbereitung in Lünen
Am Recyclingstandort in Lünen haben wir im Februar 2024 eine innovative Anlage zur voll automatisierten Probenaufbereitung von Elektroschrott in Betrieb genommen. Die neue Anlage reduziert manuelle Arbeitsschritte, steigert die Arbeitssicherheit und erhöht die Effizienz. Ein Leuchtturmprojekt des gesamten Aurubis-Konzerns.
Effizient und sicher
In Lünen läuft die Probenaufbereitung von Eingangsmaterialien wie z. B. Elektroschrott nun vollautomatisch und mithilfe modernster Robotik ab. Die Anlage liefert im Prozess der Probenaufbereitung, der bisher manuell in bis zu zwölf Arbeitsschritten durchgeführt wurde und bis zu fünf Tage dauerte, nun innerhalb von nur einer Stunde effizient und sicher verlässliche Proben für die Labore. Damit setzen wir Maßstäbe in der Recyclingindustrie, steigern gleichzeitig unsere Effizienz und verbessern die Arbeitssicherheit für unser Team.
Am Recyclingstandort Lünen werden komplexe Materialien zur Rückgewinnung von Wertmetallen wie Kupfer, Gold, Silber und Palladium angeliefert. Vor dem Recycling muss das Material beprobt werden, um den Gehalt an Metallen und deren Wert zu ermitteln und um zu entscheiden, wie es sich am besten verarbeiten lässt. Diese Fragen werden mithilfe der Analyse einer Materialprobe durch die Aurubis-Spezialisten im Labor beantwortet. Die Materialprobe muss dazu sehr fein sein und genau die gleiche Zusammensetzung wie die gesamte Lieferung haben. Beides stellt die neue Anlage sicher.
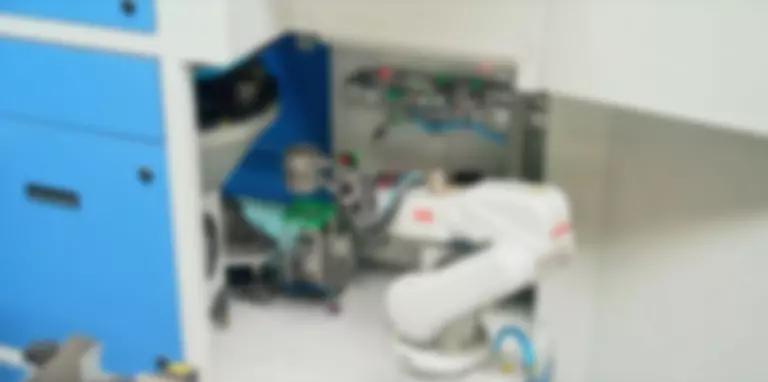
Ein Pilotprojekt für die Zukunft des Recyclings
Mit bis zu 10.000 Proben pro Jahr ist die Anlage in Lünen die leistungsstärkste ihrer Art in unserer Branche. Gleichzeitig ist sie die erste in der Aurubis-Gruppe und Vorbild für weitere Standorte. Auch für das Hamburger Werk investieren wir in eine solche Anlage, die Inbetriebnahme ist hier für Anfang 2025 vorgesehen. Die Aurubis-Werke in Bulgarien, Belgien und den USA sollen folgen. Dabei ist Elektroschrott erst der Anfang – dank der Möglichkeiten der neuen Anlage können künftig auch Kupferkonzentrate und Zwischenprodukte wie Schlacke effizient und sicher beprobt werden.
Wegbereiter der digitalen Transformation
Die Digital Factory spielt bei Aurubis eine Schlüsselrolle bei der Optimierung der Produktionsprozesse mithilfe digitaler Technologien, Automatisierung und Robotik. Die schnelle und effiziente Realisierung von Optimierungspotenzialen ist die große Stärke des Innovationsprogramms.
In einer zunehmend digitalen Welt ist es nicht mehr nur ein Wettbewerbsvorteil, sondern eine wirtschaftliche Notwendigkeit, bestehende Prozesse ständig zu überprüfen und mithilfe innovativer Technologien zu optimieren. Bei Aurubis begegnen wir dieser Herausforderung u. a. mit der „Digital Factory“ – einem internen Innovationsprogramm, das im Sinne der Unternehmensstrategie wesentlich dazu beiträgt, zum sichersten, nachhaltigsten und effizientesten Multimetall-Hüttennetzwerk zu werden.
Hinter der Digital Factory steckt ein agiles Team, das direkt an den Vorstand berichtet und Innovationen ohne bürokratische Hürden schnell in die Praxis umsetzen kann. Die Digital Factory identifiziert dazu verschiedene Projekte in den fünf großen Werken, in denen die Mitglieder gemeinsam mit den Mitarbeiterinnen und Mitarbeitern vor Ort Optimierungspotenziale ausmachen und diese dann sogleich in die Entwicklung und Implementierung von konkreten Lösungen umsetzen. Die bisherigen messbaren Erfolge der Digital Factory sprechen für sich.
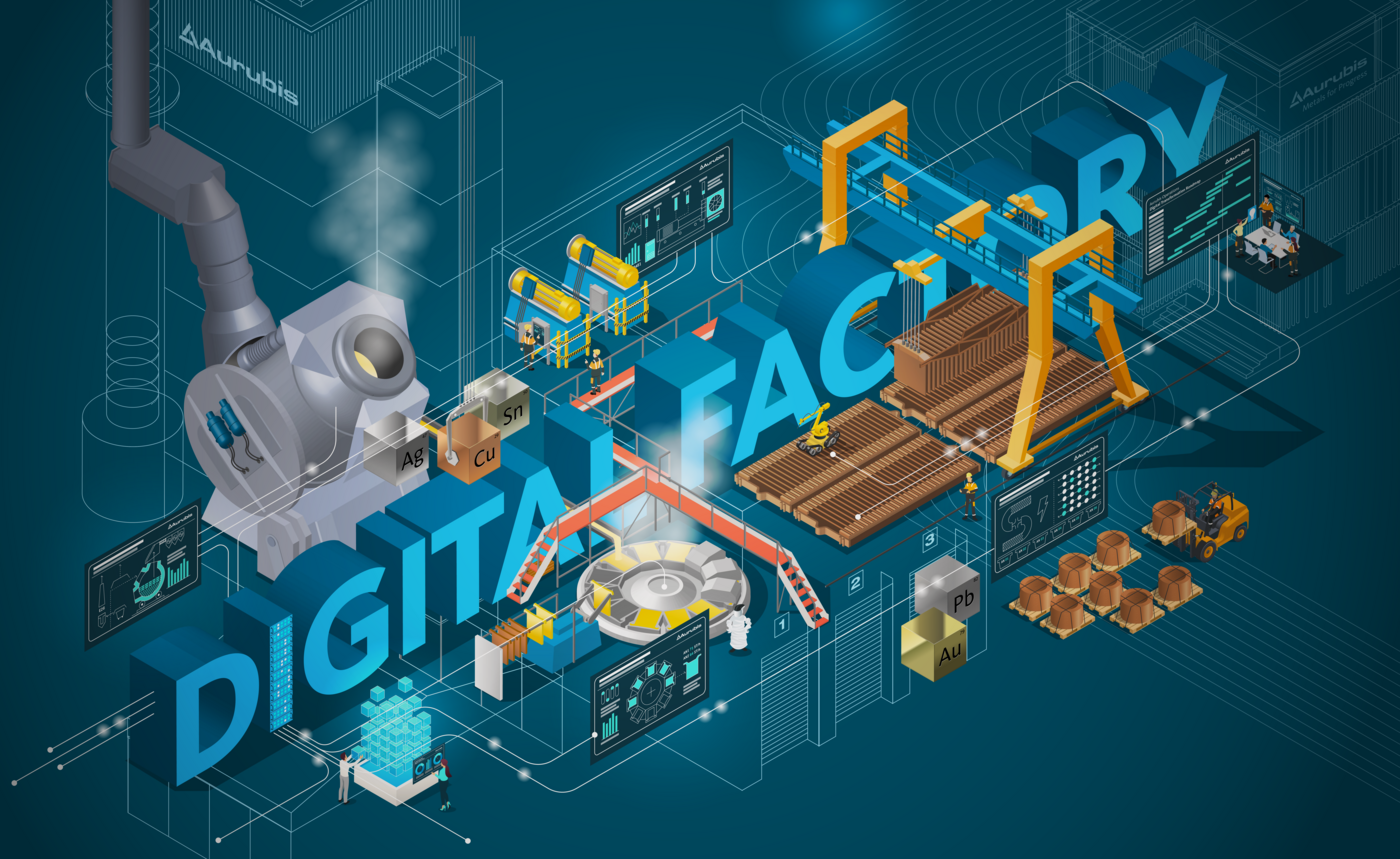
Aus Potenzialen werden Innovationen
Ein aktuelles Beispiel für die schnelle Nutzung von Optimierungspotenzialen ist ein Energiemanagementprojekt für die Dampferzeugung am Standort Hamburg: Seit August 2024 sorgt ein durch künstliche Intelligenz gestütztes System dafür, dass bei niedrigen oder gar negativen Preisen automatisch Strom für die Dampferzeugung genutzt wird. Sobald der Strompreis über dem Gaspreis liegt, produziert der gasbetriebene Kessel den Dampf. Diese Lösung zur optimierten Energienutzung hat ein Projektteam unserer Experten aus dem Energiemanagement gemeinsam mit den Kollegen aus Data Science, Data Engineering und Betriebstechnik innerhalb weniger Monate entwickelt: Unter Einbeziehung von Prozessdaten prognostiziert das System im 15-Minuten-Takt den Dampf- und Strombedarf des Werks. Gleichzeitig sorgt eine Anbindung an die Strombörse für den Abgleich der Preise. Für eine sichere Schnittstelle zwischen IT und Produktion sorgt eine Komponente der Aurubis-Tochter azeti. Diese Flexibilität bei der Energienutzung führte bereits im ersten Monat zu Einsparungen von 100.000 €, pro Jahr können so rund 840.000 € allein in dieser Anlage eingespart werden.
Digitalisierung in der gesamten Wertschöpfungskette
Die Digitalisierung bietet Aurubis enorme Chancen, die Produktionsprozesse so präzise und effizient zu gestalten, wie es bislang nicht möglich war. Von Schmelzprozessen bis hin zur Endverarbeitung werden alle Produktionsschritte von Sensoren und anderen digitalen Systemen überwacht und gesteuert. So kann der Einsatz digitaler Möglichkeiten wie künstlicher Intelligenz helfen, entlang der gesamten Wertschöpfungskette Prozesse zu optimieren, die Anlagenverfügbarkeit zu erhöhen und Wartungsaufwände zu reduzieren. Diese Transformation sorgt nicht nur für eine höhere Produktionsleistung, sondern reduziert auch den Energieverbrauch und minimiert Fehlerquellen.
Effizienter, nachhaltiger, sicherer
Die Digital Factory ist kein starres Gebilde. Unter dem Dach dieses Programms treiben unterschiedliche Bereiche gemeinsam die digitale Transformation der Produktionsprozesse bei Aurubis voran: die Digital Transformation Manager der Werksstandorte, die Bereiche Data Engineering, Data Science, Modelling and Optimization, IT Production, Group Continuous Improvement, Research & Development und die Betriebstechnik. Gemeinsam setzen wir auf Lösungen, die auf die spezifischen Anforderungen der Betriebe und Projekte in den jeweiligen Werken abgestimmt sind. Dies fördert nicht nur die Akzeptanz neuer Technologien, sondern beschleunigt auch deren Implementierung. Ein Beispiel dafür ist die Entwicklung des Condition-based Monitoring am Standort Olen, Belgien. Hier werden mittels Sensoren und Echtzeitdaten die Kühlblöcke des Schmelzofens überwacht, um potenzielle Probleme frühzeitig zu erkennen und Wartungsarbeiten präventiv durchzuführen. Dadurch können wir ungeplante Stillstände vermeiden und die Lebensdauer der Anlagen verlängern.
Zukunftsfähigkeit sichern
Durch die Vernetzung der Standorte mit Echtzeitinformationen und -analysen schöpfen wir das volle Potenzial unseres integrierten Hüttennetzwerks noch mehr aus. Sicherheit, Effizienz und Nachhaltigkeit stehen dabei im Fokus. Zudem verbessern automatisierte Prozesse und Robotik die Arbeitssicherheit und schaffen ein positives Arbeitsumfeld, das den Menschen und seine wertschöpfenden Tätigkeiten in den Mittelpunkt stellt. Wie diese Schritte in der Realität aussehen und welche konkreten Projekte umgesetzt werden, zeigen die von der Digital Factory entwickelten Zielbilder 2030+. Die Zielbilder bringen unsere Produktionsprozesse mit den umzusetzenden Innovationsprojekten zusammen und ergeben einen klaren, projektbezogenen Fahrplan für die Zukunft. Eine vereinfachte Darstellung eines Beispielzielbildes 2030+ ist weiter unten zu finden.
Das Digital-Factory-Programm wird bei Aurubis auch in den kommenden Jahren eine Schlüsselrolle bei der Weiterentwicklung und Implementierung zukunftsweisender Technologien spielen. Durch den intensiven Austausch zwischen den Produktionsstätten und die kontinuierliche Anpassung aller Prozesse an technologische Innovationen sichern wir unsere Zukunftsfähigkeit.
Zielbild Elektrolyse
Dieses Bild zeigt, wie Prozesse in der Elektrolyse künftig aussehen könnten: sicherer und nachhaltiger, mit mehr Durchsatz, weniger Wartungsaufwand und erhöhter Anlagenverfügbarkeit.
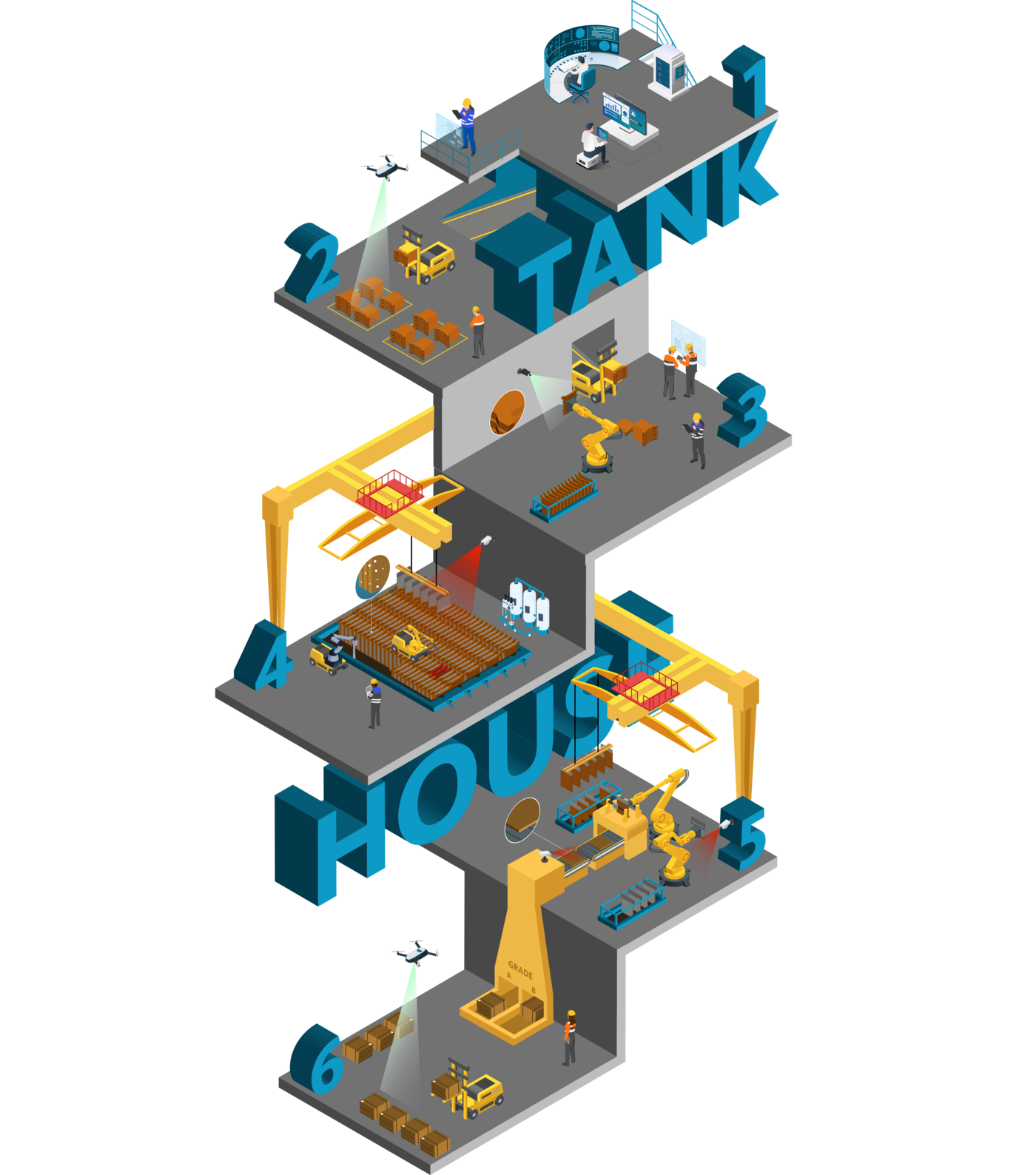
1. Steuerung und Instandhaltung
Sensor- und Kameradaten helfen, Produktionsprozesse transparent und lückenlos zu verfolgen und zu steuern.
2. Lager
Durch autonome Transporte und eine automatisierte Erkennung der Anoden steigen Durchsatz und Sicherheit.
3. Qualitätssicherung
Vorhersagen künstlicher Intelligenz (KI) und Tiefenkameras tragen dazu bei, die Prozesse zu optimieren.
4. Elektrolyse
Vom Einsetzen der Anoden bis zur Entnahme der Kathoden tragen automatisierte Produktionsschritte zu Effizienz und Sicherheit bei.
5. Kathodenmanagement
Tiefenkameras analysieren die Kathoden, um den Bedarf für Wartungen oder Prozessverbesserungen zu identifizieren.
6. Kathodentransport
Automatisierte Transportsysteme sorgen für transparente Bestände und mehr Sicherheit.